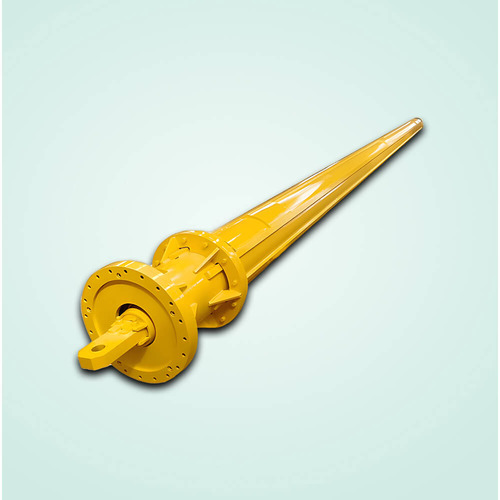
Friction Kelly Bar
Friction Kelly Bars excel in versatile drilling scenarios, utilizing friction to transmit torque and optimize performance. Their design ensures efficient drilling in various soil conditions, making them a reliable choice for foundation construction projects requiring adaptability and precision.
Here are some key features and functions of Kelly bars:
Transfer of Torque: Kelly bars are designed to transmit torque from the drilling rig's rotary drive to the drill string, allowing the drill bit or auger to rotate and penetrate the ground. They are a crucial component in the drilling process, as they ensure the effective transfer of power.
Length and Diameter: Kelly bars come in various lengths and diameters to suit different drilling applications. The length of the Kelly bar determines how deep the borehole can be drilled, while the diameter is chosen based on the size of the drilling equipment and the type of drilling tool being used.
Telescopic Design: Many Kelly bars are telescopic, meaning they consist of multiple sections that can be extended or retracted as needed. This feature allows for flexibility in drilling at various depths without the need for changing the entire Kelly bar.
Durability: Kelly bars are typically made from high-strength steel to withstand the demanding conditions of drilling operations. They must be able to endure high torque and axial loads without failure.
Compatibility: Kelly bars must be compatible with the specific drilling rig and tooling being used. Proper alignment and connection are critical to ensure efficient drilling and prevent damage to the equipment.
Maintenance: Regular inspection and maintenance of Kelly bars are essential to ensure their safe and reliable operation. Over time, wear and tear can occur, and any damaged or worn parts should be replaced promptly.
Safety: Safety precautions are vital when working with drilling equipment, including Kelly bars. Operators and workers must be trained in safe drilling practices to prevent accidents and injuries.